There are many kinds of polyester and recycled cellulose fiber blended fabrics in the market, mainly polyester viscose, polyester viscose tencel, polyester viscose modal, polyester tencel bamboo, polyester/modified polyester/viscose, etc.
Polyester includes conventional polyester, cationic dyeable polyester and polyester as the carrier of bamboo charcoal fiber, coffee silk, thermal silk, cold silk, etc., and its blended fabrics are highly complementary. When the polyester content is higher than 50%, the blended fabric can maintain the firmness, wrinkle resistance and dimensional stability of the polyester, with stiff and crisp characteristics. The addition of viscose fiber improves the air permeability, hygroscopicity and antistatic property of the fabric. Tencel (Lyser) has excellent moisture absorption, silky floatability, comfort and so on, to overcome the ordinary viscose fiber strength is low, especially low wet strength defects; Modal has the softness of cotton, the luster of silk, the smoothness of hemp, and its water absorption,
Air permeability is better than cotton, has a higher dyeing rate, fabric color bright, full; Bamboo fiber has good air permeability, instant water absorption, wear resistance and dyeing properties, but also has natural antibacterial, antibacterial, mite removal, deodorant and UV resistance functions. The application of bamboo charcoal silk, coffee silk, thermal silk, cold silk and other new fibers makes the blended fabric have a variety of functions. Polyester and recycled cellulose fiber blended fabric is characterized by smooth and smooth fabric, bright color, strong sense of wool shape, good elasticity in the hand, good moisture absorption and moderate price. It is a wool-like fabric with the advantages of wool fabric and chemical fiber fabric. It is not only the suit fabric, but also the main fabric of casual pants and trousers.
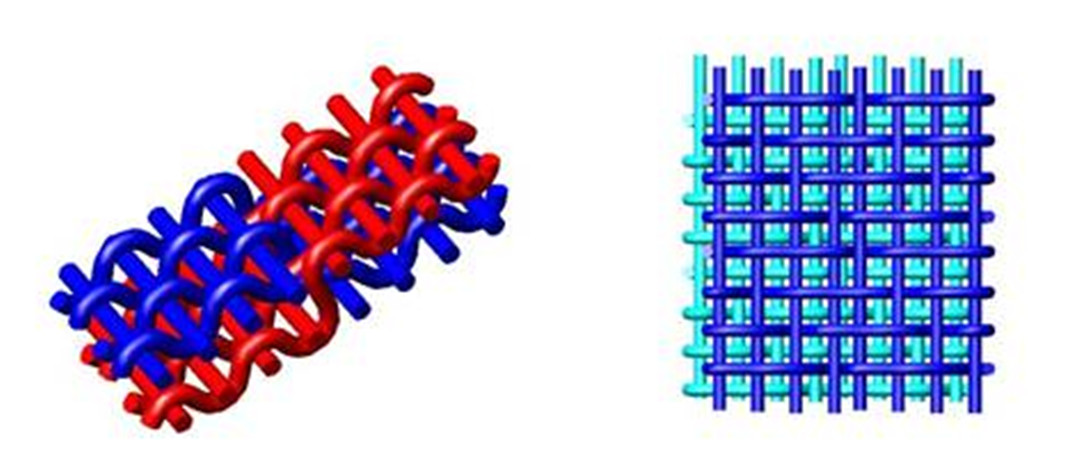
Polyester and regenerated cellulose fiber blended fabric
1. PROCESS FLOW
Polyester and recycled cellulose fiber blended fabric → grey cloth with cylinder joint → grey cloth singeing → scouring (desizing) → alkali reduction → dyeing → Setting → (soap washing → drying) → color cloth singeing → washing machine washed cloth → drying → soft finishing → dressing → calcining → pot steaming → inspection → packaging.
2. MAIN PROCESS PARAMETERS
Polyester and recycled cellulose fiber blended fabric in the spinning and weaving process due to mechanical friction, will produce a lot of hair, the purpose of hair is to singe these hairs. Fleece not only makes the surface of the fabric clean and smooth, but also can improve the fabric in the process of pilling phenomenon. The flame temperature of the hair is usually 900~1000 ℃.
Process conditions: gas singeing machine; Fuel: gasoline, natural gas; One positive and one negative flame, double-sided burning; Speed: light fabric 100~120m/min, heavy fabric 80~100 m/min; The distance between fabric and reduction flame is 0.8~ 1.0cm; Gasoline gasification capacity of 20~25 kg/h, gasification temperature ≥ 80 ℃, the use of wind pressure 9.0×103 Pa
BOILING-OUT
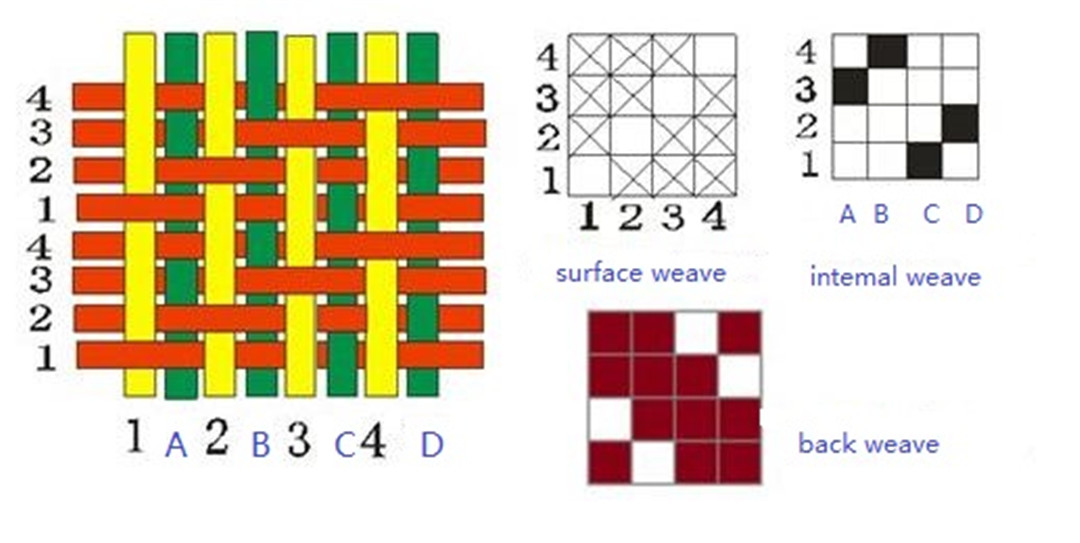
The purpose of boiling-out is to remove oils and impurities from the fibers. With caustic soda and deoiling, refining agent, boiling agent and other additives, at a certain temperature, in alkaline bath through the dissolution, degradation, melting and other effects, so that part of the fabric impurities directly dissolved in the boiling liquid; Some impurities fall off the fabric by washing due to the reduction of the binding force between swelling and fiber. Some impurities are stripped from the fabric by the dissolution of surfactants.
When alkali reduction treatment, polyester surface is corroded by alkali, its mass is reduced, fiber diameter is thinner, surface is formed pitted, fiber stiffness is reduced, eliminate the northern light of polyester silk, and increase the gap of fabric interweaving point, make fabric feel soft, soft luster, improve moisture absorption and perspiration. Alkali decrement is used to improve the softness and pilling properties of polyester by the peeling effect of caustic soda.
Process conditions: caustic soda 10~15 g/L, temperature 125 ℃, treatment time 40 min.
Two-step dyeing, disperse dye, high temperature reactive dye dyeing in the same cylinder, temperature 130 ℃, holding time 30~40 min, cooling to 95 ℃, holding time 40~60 min, two-step method is suitable for light and medium color dyeing.
Disperse dyes and cationic dyes were dyed in the same bath, the temperature was 120~130 ℃, and the holding time was 40~50 min. Medium temperature reactive dye dyeing, temperature 60 ℃, holding time 40~60 min.
FABRIC SETTING
Fabric after heat shaping can improve dimensional stability, even in the wet and hot dyeing and finishing processing conditions and after the wearing process is not easy to deformation.
The temperature is 180~190 ℃, the speed is 30~40 m/min, the overfeeding is 1%~ 3%, the setting time is 40~50 s.
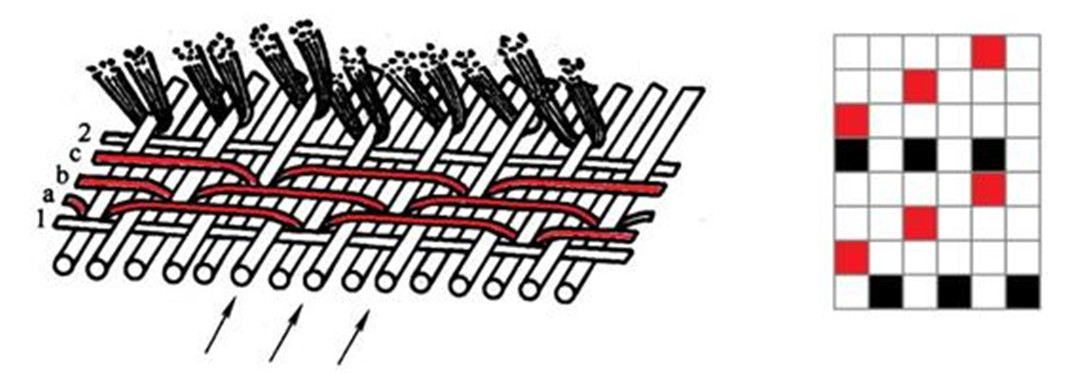
SOFT FINISH
In the dyeing and finishing process of textile, after a variety of chemical agents wet and hot treatment and mechanical tension and other effects, not only the organizational structure changes, and can cause the feel stiff and rough, soft finishing can make up for this defect, make the fabric feel soft. Chemical soft finishing is the use of softener to reduce the coefficient of friction between fibers to obtain soft effect.
Hydrophilic amino silicone softener 20~50 g/L, antistatic agent 10~15 g/L, temperature 170~180 ℃, speed 35~45m/min, overfeed 1%~ 3%.
1. The blended fabric of polyester and regenerated cellulose fiber shall be dyed dark colors such as navy blue and black, and the color fastness to wet rubbing shall meet the requirements of Grade 1 or more than Grade 3 of the national textile quality standard. Special printing and dyeing process shall be adopted. If the blended fabric contains tensilk, after heavy alkali reduction treatment dyed dark color, wet friction color fastness is slightly low, some only 2-3 level, can only meet the national quality standards of textile qualified products.
2. When dyeing coffee, khaki, grape purple, red and other bright colors and light colors, the color fastness to light and sweat light compound color fastness is slightly poor, only reaching about level 3.
3. Pay attention to the slip of the lightweight blended fabric and the interweave, some of which do not reach the national quality standard of ≤ 0.6cm.
Dyeing process of polyester and eclaimed cellulose weft elastic fabric
Polyester and regenerated cellulose fiber blended weft elastic fabric is a developing trend, and more and more recognized by consumers. The warp yarn of the fabric is polyester and recycled cellulose fiber blended yarn or blended yarn and polyester yarn arranged in a certain proportion according to the style requirements. The weft yarn is polyester covered spandex yarn or cationic polyester covered spandex yarn.
Technological process
Polyester and recycled fiber blended elastic fabric → grey fabric with cylinder → singeing → boiling-out (desizing) → alkali reduction → dyeing → shaping → soft finishing → dressing → calendering → pot steaming.
DYEING
Polyester/recycled fiber/polyester spandex elastic fabric is dyed with disperse dye and reactive dye two-bath process, disperse dye on polyester and spandex at the same time, reactive dye on the recycled fiber.
Polyester/recycled fiber/cationic polyester spandex elastic fabric is dyed in two baths. The first bath is dyed with cationic dye and disperse dye in the same bath. Cationic polyester is dyed with cationic dye, polyester and spandex are dyed with disperse dye, and cationic polyester is also dyed with cationic dye. The second bath is regenerated with reactive dye.
Prone to quality problems
Blank cloth width, according to the actual situation of weaving and dyeing shrinkage rate reasonable design, to meet the requirements of finished product width.
If the process conditions are not properly controlled, the brittleness and damage of spandex fibers will be caused in the process of singeing and alkali reduction of thin fabric, which will seriously affect the zonal strength of fabric.
Wet friction color fastness and dry cleaning resistance is poor, the wet friction color fastness of medium dark color is 2~3 or 2, and the color fastness to washing is about 3.
Post time: May-30-2023